I have been super busy, and I still have a rant percolating, especially about those brain dead college student and their "professional Activist" handlers.
I wanted to get a post up last Sunday but I wound up sleeping 13 hours...I guess I am was tired.
These fake parts are a big deal, this is how we keep our "Airworthiness" Certificate on our airframes and engines. Several airlines got bit hard by these fake parts and it causes problems, especially when the cost of parts go up and there are supply chain issues so airlines are looking for parts wherever they can to keep their planes flying.
I have blogged before about the "Various parts issues" that planes are having.

Forged paperwork helped AOG Technics pass off thousands of apparently used CFM56 parts as new.
The Canadian regional jet operator’s emailed request was routine—the airline needed six check valves. Florida-based parts broker Sofly Aviation Services went to work, soliciting quotes from other vendors. The distributor also went looking for valves in “as-removed” condition, meaning they have not been inspected or tested.
Sofly soon received a quote for new valves at $3,850 per valve. The quote included an FAA 8130-3 airworthiness approval document, or tag, issued by the part’s Arizona-based supplier indicating the valves were new—a common move to reassure would-be parts purchasers before they buy. Sofly also found a source for as-removed valves.
Sofly had everything it needed. The vendor bought as-removed valves for $300 each. It then relabeled them as new and sold them to the Canadian carrier—at new-part prices—supplying the 8130-3 tag from the new-part quote to back the deal.
The fraudulent transaction, one of several that took place over seven years, helped set the stage for guilty pleas by two Sofly executives in a case brought by the U.S. Justice Department, court filings show. The case against Sofly, which ended in the March 2024 pleas, underscores the challenging—some would argue impossible—task facing a recently formed supply chain integrity coalition.
Engine manufacturers GE Aerospace and Safran and their CFM International joint venture spearheaded formation of the Aviation Supply Chain Integrity Coalition (ASCIC) in February. Airbus, American Airlines, Boeing, Delta Air Lines, StandardAero and United Airlines are also part of the group.
The effort is a direct response to a more well-known records falsification scandal. UK-based distributor AOG Technics sold thousands of engine parts with forged regulatory approvals—8130-3s and European Union Aviation Safety Agency (EASA) Form 1s—until one customer caught on last summer (Inside MRO November 2023, p. MRO20).
Much like the Sofly case, forged mandatory paperwork appears to have been the key to AOG Technics’ fraud.
The scandal came to light last July when technicians at TAP Maintenance & Engineering flagged some GE CF6 bushings purchased from AOG Technics. Paperwork shipped with the parts suggested they were new, but the TAP mechanics suspected otherwise.
GE confirmed that documentation provided with the parts was fraudulent, and a subsequent FAA notice detailed some of the findings. The document listed the part as a “bushing.” But GE’s common terminology for the form is “bushing shrd (IGV),” states the FAA notice sent last September. Language also was missing from the form’s “user/installer responsibilities” block. “GE does not remove boilerplate language from the FAA Form 8130-3,” the FAA notice adds. The FAA also flagged boxes not grayed out on the CF6 forms that should be grayed out “for new articles.”
TAP soon found more AOG-supplied parts with forged documents.
CFM, GE and Safran alerted customers and regulators immediately, and both EASA and the UK Civil Aviation Authority issued notices in early August. A month later, the companies—eager to identify the issue’s scope and receiving little assistance from the authorities—filed suit against AOG, demanding transaction records and other possible pieces of evidence.
In all, some 200 forged documents shipped with thousands of otherwise legitimate parts, ranging from nonserialized fasteners to turbine blades, were discovered in the supply chain. Some made it into engines.
The UK Serious Fraud Office in early December opened a criminal investigation and raided AOG Technics’ London offices.
While hardly the first instance of criminal activity related to aviation parts, the AOG Technics case grabbed global headlines—and caught suppliers’ attention. CFM pledged last fall to dig into what, if anything, industry can do to reduce opportunities for parts fraud. The coalition was formed to lead that effort.
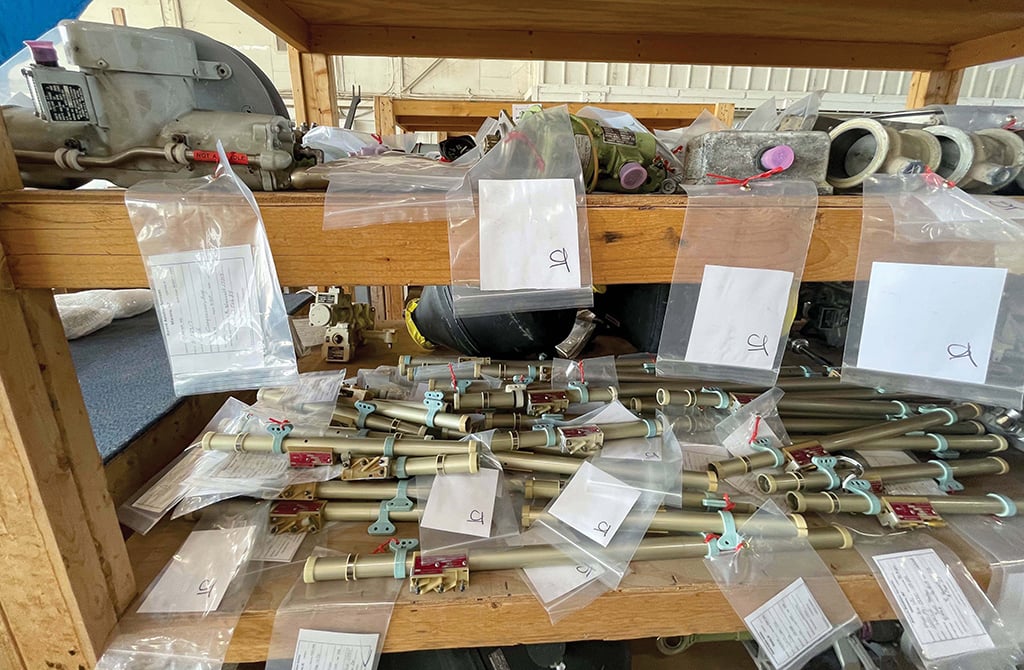
Coalition representatives meet every other week. In between, they seek input from other subject matter experts—a list that has been growing—coalition co-chair and former NTSB Chair Robert Sumwalt says.
“As we learn of other entities and organizations that can provide value, we’re bringing them in,” he says. “There has been a lot of interest from people in the industry that are coming to us saying that they’ve got something to offer.”
One source providing input is the Aviation Suppliers Association (ASA). Aside from serving as the primary industry voice for parts providers and distributors, the ASA also developed a standard, ASA-100, and a related audit program for companies that choose to comply with the FAA’s voluntary industry distributor accreditation laid out in Advisory Circular (AC) 00-56B.
Introduced in 1996 via the original AC 00-56, the FAA’s program was industry’s response to a wave of concern over unapproved—then often called “bogus”—parts. The ASA followed with ASA-100, providing a standard, third-party program to match.
More than 760 companies are ASA-100 certified. Other regulators, including EASA and the Civil Aviation Administration of China, have similar, voluntary programs. While they can add a level of legitimacy to a distributor’s resume, such programs cannot prevent crime.
“We will always have fraud,” ASA President Michele Dickstein says. “We need to make sure that we have increased the safeguards to protect against fraud and that we have the reaction skills to bring it to light very quickly if it happens.”
Sarah MacLeod, executive director of the Aeronautical Repair Station Association, sees the AOG Technics case as instructive. Forged paperwork got suspect parts to MRO shop floors, but calling a used part new did not fool a technician’s wary eye.
“A knowledgeable technician can pick up a part and go through a technical evaluation of whether or not it is any good,” MacLeod says. “We have agencies that are hell-bent on having their pieces of paper and only their pieces of paper. That opens another avenue for criminal activity and makes it easier for them, because we’re looking for paperwork. A piece of paper doesn’t make a part airworthy.”
Airworthiness is determined not by some approved manufacturing or repair process backed by documentation but rather by a combination of circumstances, she adds. For example, one airworthiness directive (AD) can render a new, genuine engine part sitting on a shelf with proper paperwork unusable.
“I can have the best paperwork in the world, and the FAA issues an AD against the part. Guess what? I’ve got an approved part that I can’t install,” she says. “So what can we do? Educate people to look beyond the paperwork. Educate them on what they are doing, why they are doing it and the cost of failure.”
While preventing individuals from committing fraud is a high bar, the coalition is confident that it can help strengthen parts distribution protocols.
“I think everybody is aligned with the notion that what happened with AOG Technics is totally unacceptable and cannot be allowed to happen again,” Sumwalt says.
Both Sumwalt and ASCIC co-chair John Porcari emphasize that their main goal is to balance thoroughness with expediency. Understanding how the aircraft supply chain and programs such as the FAA’s voluntary distributor accreditation program works is the first step.
“It’s fair to say we’re deep into the research phase at this point,” says Porcari, a former U.S. Transportation Department deputy secretary.
From there, “we’re going to let the facts drive where we go,” Sumwalt says. “We want to learn the issues.
“The next phase will be to draft a report,” he adds. “We’re going to take our time and do it right. That said, we’ve got an aggressive time frame to make sure that we get these recommendations out in a timely manner.”
The coalition plans to have a report ready by year-end.
“The common goal is meaningful, actionable measures that can come out of this,” Porcari says. “This is a coalition of the committed. On the safety and quality assurance side, there’s always more work you can do. I think this is an acknowledgement of that.”
One of my former shipmates is heavily involved in this at Safran!
ReplyDelete